PRODUCTS Categories
CONTACT US
- Phone:
- 86 17344894490
- Tel:
- 86 17344894490
- Email:
- business@signialuminium.com
- Add:
- Zhengzhou, Henan, China.
Company News
Anodized aluminum profile
Time :2019-11-13
The surface treatment process of aluminum profiles is various, and the oxidation treatment process of aluminum profiles is mainly introduced here. As we all know, the oxidation treatment process of aluminum profiles is divided into two major categories: anodizing and chemical oxidation, and there is a big difference between the two.
Anodizing refers to the process of forming an aluminum oxide film on the surface by electrolysis to place the aluminum profile under the corresponding electrolyte and specific process conditions, which is called anodizing of the aluminum profile. Anodization, if not specifically indicated, generally refers to anodization of sulfuric acid.
Chemical oxidation refers to the treatment of the surface of an aluminum profile with a chemical medium, and the surface of the aluminum is oxidized by a chemical reaction to form a stable rust-proof oxide film, which is called chemical oxidation treatment of the aluminum profile. The chemical oxidation process can be divided into two major categories: alkaline oxidation and acid oxidation.
There are three differences between the two treatment methods:
(1) Anodizing is carried out under high voltage, which is an electrochemical reaction process; chemical oxidation does not require electricity, but only needs to be immersed in the syrup, which is a pure chemical reaction.
(2) The time required for anodizing is very long, often takes several tens of minutes, while chemical oxidation takes only a few tens of seconds.
(3) The thickness of the oxide film formed by anodization is about 5-20 microns (hard anodized film thickness can reach 60-200 microns), with high hardness, good heat resistance and insulation, and corrosion resistance. It is higher than the chemical oxide film, porous and has good adsorption capacity. The film formed by chemical oxidation is only about 0.01-0.15 micrometers, the softness is not wear-resistant, and the corrosion resistance is lower than that of the anodized film, and it is generally not suitable to be used alone.
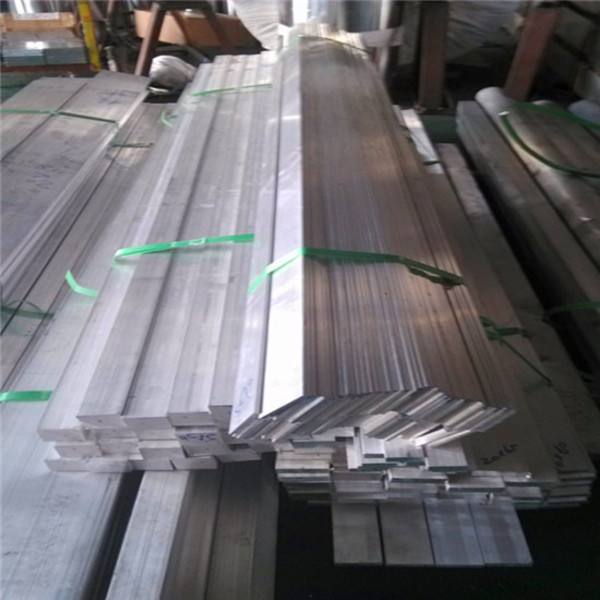
Anodizing refers to the process of forming an aluminum oxide film on the surface by electrolysis to place the aluminum profile under the corresponding electrolyte and specific process conditions, which is called anodizing of the aluminum profile. Anodization, if not specifically indicated, generally refers to anodization of sulfuric acid.
Chemical oxidation refers to the treatment of the surface of an aluminum profile with a chemical medium, and the surface of the aluminum is oxidized by a chemical reaction to form a stable rust-proof oxide film, which is called chemical oxidation treatment of the aluminum profile. The chemical oxidation process can be divided into two major categories: alkaline oxidation and acid oxidation.
There are three differences between the two treatment methods:
(1) Anodizing is carried out under high voltage, which is an electrochemical reaction process; chemical oxidation does not require electricity, but only needs to be immersed in the syrup, which is a pure chemical reaction.
(2) The time required for anodizing is very long, often takes several tens of minutes, while chemical oxidation takes only a few tens of seconds.
(3) The thickness of the oxide film formed by anodization is about 5-20 microns (hard anodized film thickness can reach 60-200 microns), with high hardness, good heat resistance and insulation, and corrosion resistance. It is higher than the chemical oxide film, porous and has good adsorption capacity. The film formed by chemical oxidation is only about 0.01-0.15 micrometers, the softness is not wear-resistant, and the corrosion resistance is lower than that of the anodized film, and it is generally not suitable to be used alone.